Strength is a term used most often in the construction industry. It’s what builders, engineers, and developers look for when choosing materials. But not all TMT bars are built the same. The manufacturing process is one of the biggest factors determining the strength, durability, and reliability of TMT bars. Hot billet rolling is widely recognized as the best method for producing high-quality TMT bars that meet the demands of modern construction. It refines the grain structure, eliminates impurities, and produces bars that offer consistent strength, flexibility, and corrosion resistance.
Many claim to be strong, but their quality is only as good as the process used to make them. India is expanding rapidly, and the demand for reliable construction materials is growing with it. The industry is set to grow at 6.2% annually from 2025 to 2028.
It is easy to complete more projects using cheaper materials, but cutting corners on quality leads to higher maintenance costs, safety risks, and loss of reputation. Builders today are under more scrutiny than ever. The newspaper will confirm that daily. It is shameful but real. Consumers and regulatory bodies actively monitor the quality of materials used in construction. A single mistake in choosing subpar TMT bars can damage a company’s goodwill, affecting future projects and customer trust.
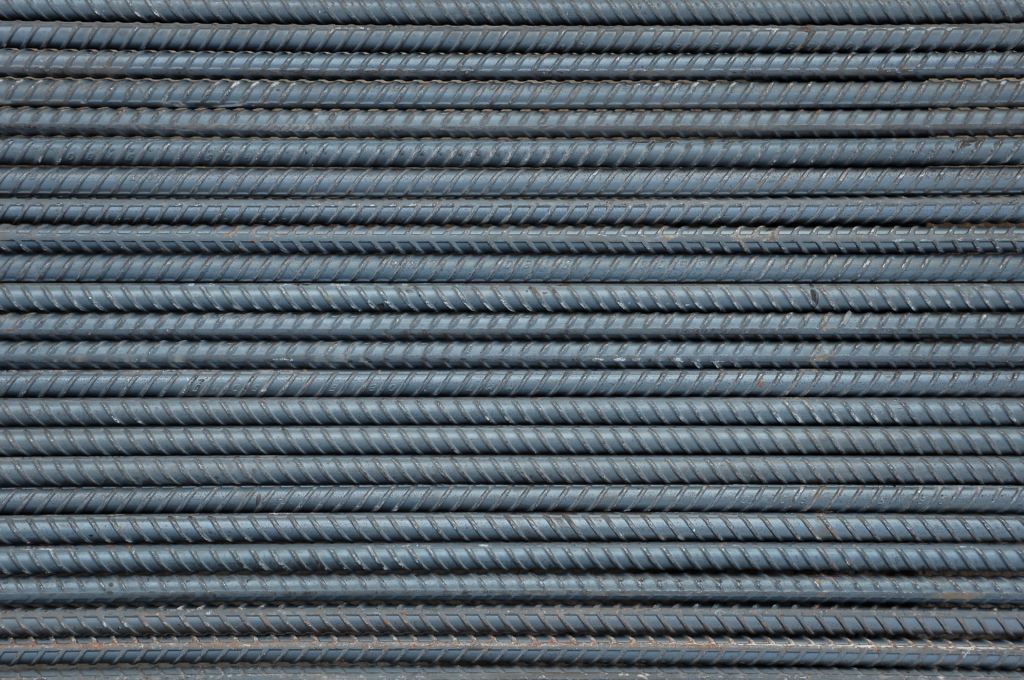
Simply put, the hot billet rolling process eliminates common problems found in low-quality bars, making them stronger, more durable, and better suited for high-rise and infrastructure projects.
The Problems With Subpar TMT Bars
Many TMT bars in the market come from manufacturers that rely on re-rolling scrap metal instead of fresh billets. While this keeps production costs low, it creates serious issues for construction projects.
Common problems with low-quality TMT bars
✔ Inconsistent strength – Weak spots in the bars create vulnerabilities in the structure.
✔ High corrosion rates – Impurities in scrap metal cause faster rusting, especially in humid and coastal areas.
✔ Brittle composition – TMT bars that crack easily make on-site work difficult and compromise safety.
These issues are not noticeable immediately. They reveal themselves over time when the structure is under stress, leading to unexpected repair costs, compromised safety, and structural failures.
Why Hot Billet Rolling Produces Better TMT Bars
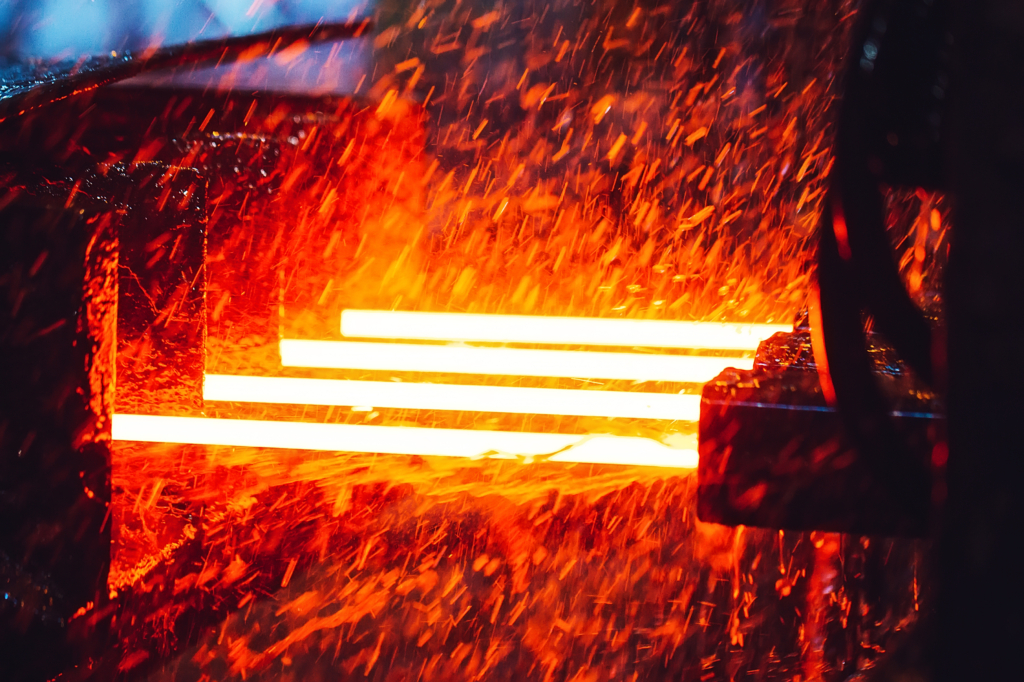
The quality of TMT bars starts with the raw material and the rolling process. Using fresh billets instead of scrap makes a major difference in strength, consistency, and corrosion resistance.
Fresh Billets Instead of Recycled Metal
Using only direct billet rolling you can avoid the impurities found in re-rolled scrap. This means:
✔ Better load-bearing capacity for high-rise and heavy-duty structures.
✔ More consistent chemical composition across all batches.
✔ Lower risk of corrosion, even in challenging environments.
Precise Heating for Strength and Flexibility
TMT bars need to be strong without being too rigid. Heating the billets at 1100-1200°C allows the steel to maintain its structural integrity without developing internal stress fractures.
Controlled heating prevents
✔ Over-hardening, which causes brittleness and cracking.
✔ Uneven cooling, which creates weak zones in the bar.
✔ Loss of flexibility, making the bars harder to work with on-site.
Hot Billet Rolling That Prevents Structural Weakness
Each billet passes through a series of high-precision rolling mills, refining its grain structure and eliminating internal defects. This step is critical for producing TMT bars that can withstand high stress without failing.
Key benefits of Hot Billet Rolling
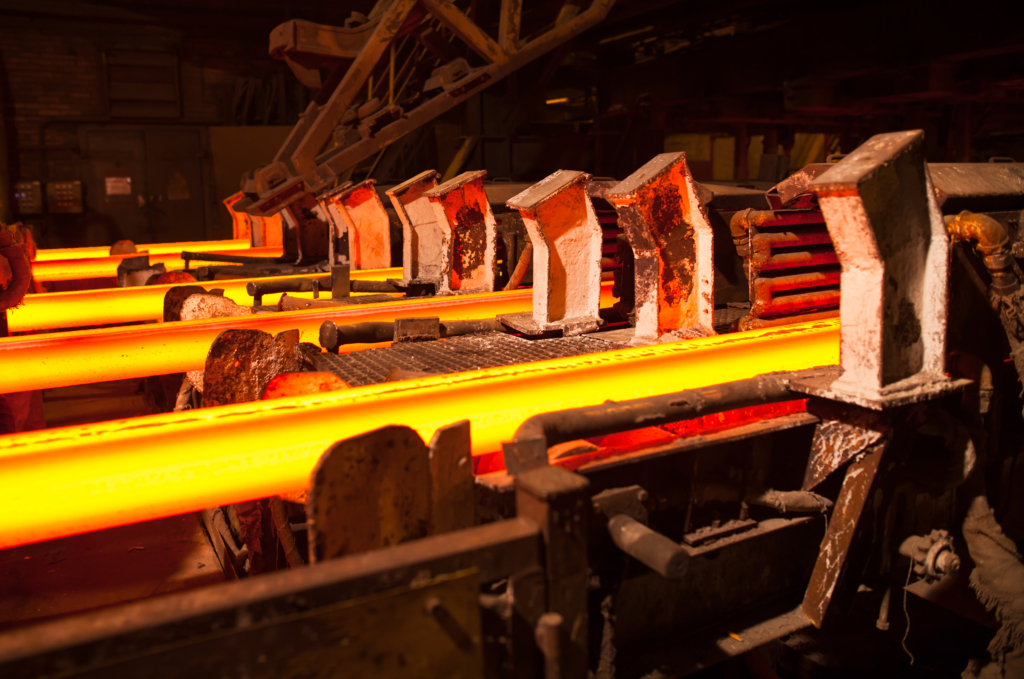
✔ Uniform strength across the entire length of the bar.
✔ Higher fatigue resistance, making them ideal for long-term projects.
✔ Increased workability, allowing smooth bending and welding.
Quenching and Self-Tempering for Durability
After rolling, the bars undergo a quenching process, during which they are quickly cooled to harden the outer layer while keeping the core flexible. This combination of strength and ductility makes TMT bars suitable for earthquake-resistant structures.
✔ Higher shock absorption for seismic-prone areas.
✔ Better elongation properties, reducing material wastage.
✔ Longer lifespan with reduced chances of surface cracking.
How Jumbo TMX’s Hot Billet Rolling Solves Common Construction Problems
1. Why do some TMT bars develop cracks over time?
This usually happens because of impurities from recycled scrap. We avoid this issue by using fresh billets, resulting in a cleaner, stronger, and more reliable product.
2. Why do some bars rust faster than others?
The presence of excess phosphorus and sulfur in re-rolled bars accelerates corrosion. By maintaining strict quality control over raw materials, our bars have superior rust resistance, even in coastal regions.
3. What makes Jumbo TMX bars easier to work with on-site?
Some TMT bars are too rigid, which makes bending and welding difficult. Our controlled rolling and quenching process produces bars that are both strong and flexible, reducing breakage and material wastage.
Why Leading Developers Choose Jumbo TMX
Builders and contractors who work on large-scale projects cannot afford material failures. Strength, flexibility, and long-term performance matter. That is why they choose Jumbo TMX hot billet rolled TMT bars.
✔ Only fresh billet rolling, no re-rolled scrap steel.
✔ Every batch tested for mechanical strength and consistency.
✔ Used in infrastructure projects that require long-term durability.
✔ Engineered for earthquake-resistant, high-rise, and industrial applications.
A poorly made TMT bar may pass a basic test, but it won’t hold up under real-world conditions. Developers who want to build structures that last don’t take chances on quality and choose only Jumbo TMT Bars.
Cutting Corners Costs More in the Long Run
Saving money on materials by choosing low-cost TMT bars might seem like a smart decision, but it rarely works out that way. When bars corrode or develop cracks, the repair and reinforcement costs far exceed the initial savings. In some cases, poor-quality materials can even lead to structural failure and legal consequences.
More than that, customers and investors today are more informed than ever. They research the materials used in projects, check for transparency, and demand higher standards. A company that uses subpar materials risks losing its credibility, which affects future business and trust in the market.
At Jumbo TMX, we believe that cutting corners in material quality is not an option. Our bars are built for safety, durability, and performance because we know that builders and developers need materials they can rely on, not just for today but for decades to come.
When it comes to structural integrity, there are no second chances. Leading developers know that and that’s why don’t take risks, they choose Jumbo TMX.